A bulkhead is a barrier between land and water commonly constructed in fresh and saltwater environments. They can be made from various materials, including concrete and steel. Treated lumber is also popular for its natural appearance and affordability.
Bulkhead plating is fabricated in several stages before installation. This helps prevent stress concentration in corners, which could cause a loss of structural integrity. For more information just visit Dock Lifts Charleston SC to proceed.
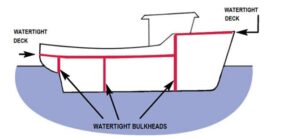
Bulkheads are structural support walls that separate spaces in a vessel, providing stability and minimizing the risk of structural failure. These structures are often made of concrete but can also be constructed from wood or composite materials. They are used in various applications, including separating different compartments within ships and other structures, preventing flooding, or providing water control in industrial settings.
Bulkheads’ main function is to prevent coastline erosion by creating a distinct separation between land and sea. Typically, these structures are installed along the transition between natural or reclaimed shorelines and port basins. Bulkheads can also be used on land as retaining walls to keep soil from traveling down inclines or to prevent flooding.
They also serve to protect boats from colliding with a shoreline. Because these structures are often built from sturdy material, they can withstand considerable force and help to keep boats safe from the water’s edge. They are particularly useful for large vessels such as submarines, ships, or barges that must remain stable when moving in water.
While bulkheads can be a valuable tool for controlling coastal erosion, they can cause problems for neighboring properties in some locations. In these cases, bulkheads may direct wave energy to other areas of the bluff or beachfront, leading to “flanking” that increases erosion rates on neighboring waterfront properties. This effect is sometimes hard to detect because erosion generally occurs over a long period but can be accelerated by storm activity or excessive wave action.
Erosion caused by bulkheads can result in loss of beachfront property and repercussions for adjacent properties that cannot absorb the wave energy and the sand that has been washed away. Suppose you notice that your bulkhead is eroding. In that case, it’s important to seek technical advice on alternatives for shoreline protection that will be less damaging to your property and the ecology of Spa Creek.
If your bulkheads are showing signs of failure, such as cracks in the concrete or gaps in the berm, it’s important to act quickly. If left unattended, these issues can lead to berm failure that will wash out backfill and increase erosion on the property behind your bulkhead—correcting this problem by adding riprap or bags of dry concrete mix to the sheathing or adding a French drain below the bulkhead to facilitate drainage and reduce water pressure on the structure.
Bulkheads are a crucial piece of waterfront infrastructure, especially in areas where erosion is a real threat. Erosion is the natural process of water slowly eroding soil, which can quickly chip away at the amount of land your property has. Without the protective barrier of a bulkhead, this can lead to the loss of not just inches but feet of land. Bulkheads prevent this by retaining soil and keeping it above water, even after flood or high tide events.
Aside from their functional advantages, bulkheads can also provide a great aesthetic appeal for your waterfront property. If you want to enhance the visual appeal of your home’s bulkhead, it may be worth capping it with a new material. This is a simple way to add a clean, modern look to your home’s existing bulkhead and can instantly improve the appearance of your waterfront.
In addition, bulkheads help to make the shoreline safer for anyone who wants to use it. How often have you walked along the shoreline and nearly tripped on a rock or other obstruction? With the added stability of a bulkhead, your walkways will be much clearer and easier to navigate.
Several important steps are needed to ensure the best results when constructing a bulkhead. First, the site must be prepared by clearing and preparing the foundation. Once the foundation is in place, the framework for the bulkhead can be constructed, following the design specifications. Finally, the panels or walls are installed within the framework to complete the bulkhead.
Once your bulkhead is in place, it’s important to maintain and protect it from debris that can cause damage. If you notice that a section of your bulkhead has become loose or damaged, it’s important to contact a professional right away. They can assess the damage and determine whether or not your bulkhead is still in good shape.
If your bulkhead is deteriorating, it may be time to replace it. To do so, finding a qualified contractor who can assist you is important. Before hiring someone to complete the work, you should ask for references and check their record with the Better Business Bureau. Choosing the right contractor can ensure that your bulkhead lasts for years.
Bulkhead doors are a great way to add style and functionality to your home or business. They’re ideal for basement access or egress and accommodate large storage items like hot water tanks, pool tables, and furniture. They also help to prevent moisture and debris from entering the basement. The door is designed with a high-quality, heavy-duty seal that can withstand years of use. The ClamDoor is easy to install and requires no special tools. This means you can save money on installation costs and get your new bulkhead door up and running quickly and easily.
A high-quality, secure bulkhead door deters burglars from gaining access to your home or business. Keeping the door closed will also help to keep rainwater and other weather elements from seeping into your basement or crawl space, which can cause structural damage that’s expensive to repair.
Another advantage of a bulkhead is that it’s a great space to express your style and flair. You can paint it a contrasting color or add a decorative touch with metal and timber-look wallpaper. If you’re not a fan of wallpaper, consider painting your bulkhead a more neutral color that will complement the rest of your room.
Before installing your bulkhead, clean off any existing concrete foundation. You can do this by using a grinder fitted with a cutoff wheel. Then, you can remove the existing bulkhead doors by removing their hinge pins. Once the bulkhead opening is clear, you can install the doors by placing a 2×6 pressure-treated sill across the bottom of the bulkhead opening. Next, you can apply a thick bead of silicone sealant along the flashing at the top of the door. Finally, you can set the bulkhead’s metal header underneath the flashing and press it into the silicone sealant.
Once the bulkhead is installed, it’s important to avoid over-tightening or screwing in the flange nuts and gasket mating surfaces. This will cause the flange nut to hurry out of place and may lead to leaks. It’s also important to use supports to support pumps or piping so they don’t excessively stress the bulkhead’s gasket.
Bulkheads are easy to install and usually come in a few different types. Some are flat and corrugated, while others are round or wrap around. Flat bulkheads don’t sacrifice deck space and are often used as support for pallets and other materials, while round and wrap-around bulkheads help keep a boat in place and can be equipped with side rail kits and panels. They can also be DOT or non-DOT-rated.
Depending on the type of bulkhead you choose, there are various materials you can use to construct them from. Pressure-treated wood is a common option, but vinyl and steel are also popular. A skilled professional can advise you on the best material for your needs and the surrounding area.
If your bulkhead shows signs of wear and tear, it’s time to call a professional for repairs. Sometimes, this can be as simple as a quick patch job or installing additional helical tiebacks. In other cases, a complete replacement of the bulkhead is in order.
When installing a new bulkhead, it is important to ensure the fit is tight and secure. If water leaks through the bulkhead, it can cause damage to the underlying structure and lead to unintended consequences for you and your neighbors.
Installing the gasket properly is the easiest way to ensure your bulkhead is watertight. Always install the gasket on the flange side of the bulkhead, not the nut side. This will prevent sand and other debris from breaking down the seal. Also, clean the flange and bulkhead before putting in the gasket.
Another way to protect your bulkhead is by ensuring that the ground behind it stays dry. When water accumulates behind a bulkhead, it can create a sinkhole and even damage the underlying foundation. Bulkheads can be fitted with drainage pipes to help keep groundwater away from the area and minimize erosion and other problems.
A waterfront without a bulkhead is prone to erosion and can quickly lose not just inches but entire feet of land. Suppose your property is located alongside a lake, river, or other body of water. In that case, it’s worth calling a certified bulkhead specialist to see if a bulkhead is in your best interests.